A pipe organ is a singular musical instrument that is subdivided into divisions with names such as Great, Swell, Choir, Solo and Pedal. The division names can sometimes appear in French (Grand-Orgue, Positif, Récit, Bombarde and Pédale), in German (Hauptwerk, Brustwerk, Positiv, Schwellwerk, Pedal) or other languages. Each division is made up of stops, with each stop intending to represent a single tone colour or sound such as a flute or an oboe. For the most part, each stop equates with one rank, meaning that each stop has one pipe for each note on the keyboard or pedalboard. Some stops have more than one pipe per note or more than one rank: a mixture stop can have several ranks per note while undulating stops such as a Flute Celeste will generally have two ranks.

Each rank is associated with a pitch (16’, 8’, 4’ and so on) which corresponds to the note sounded by the rank’s longest pipe. In the case of an open pipe, the length of the pipe from the mouth to the top of the pipe corresponds to the pitch. The length of the c1 pipe of an open 8’ stop for example is approximately 8’ from the mouth to the top of the pipe. The conical pipe foot adds perhaps 18” for a total pipe length of approximately 9’6” for an 8’ pipe. Stopped pipes – with a wooden stopper or a felted metal cap over the top of the pipe – are almost half the length of an equivalent open pipe. For example, the c1 pipe for a Bourdon 8’ is roughly 4’ long without the pipe foot.
A stop at 8’ pitch will correspond with the pitch of a piano, while a 16’ stop will sound one octave lower, a 4’ stop will be one octave higher and a 2’ stop will be one octave higher still. Large organs will have a few 32’ stops – the bottom octave of such stops is more felt in the pit of the stomach than heard – while the very smallest pipes in an organ will have a pitch of 1/16’. Some organ stops have fractions in their pitches and produce tones that have an interval relationship with the unison pitch, giving rise to some unique synthetic colours. For example, a Nazard 2-2/3’ sounds one octave plus a fifth higher than unison pitch and when combined with an 8’ flute, produces an elegant and haunting solo voice.
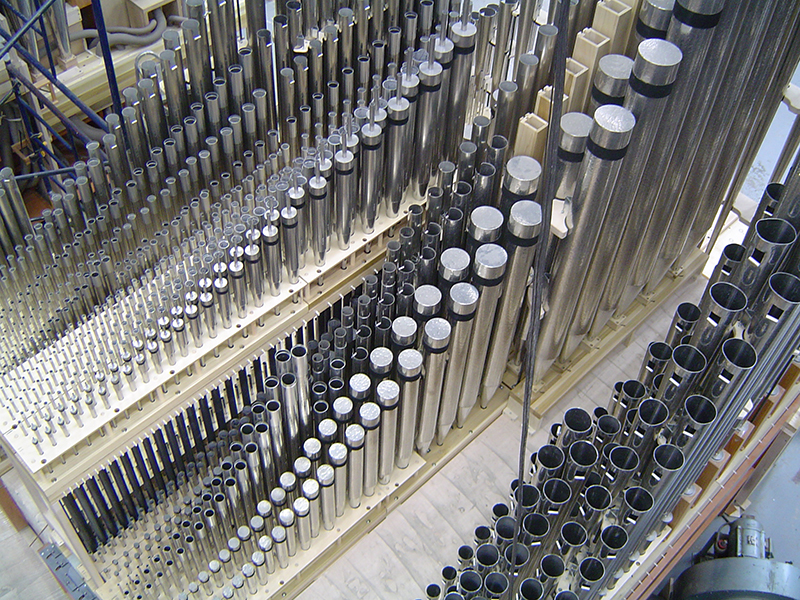
Organ pipes can be divided into two general families: flues and reeds. Flue pipes make up about 80% of an organ’s pipes and are built like whistles with the production of tone taking place at the pipe’s mouth. Reed stops produce sound in the pipe’s boot where a metal tongue vibrates against a brass shallot; this buzzing sound is then amplified by the pipe’s resonator. Depending on the desired sound, the shape of the shallot and resonator can vary widely. Organ pipes are generally built out of alloys using largely tin and lead in varying proportions with trace quantities of other metals mixed in for additional rigidity. Organ pipes can also be made from wood or zinc, usually for tonal reasons.
Organ pipes sit in rows on wind chests that resemble thick tables; the chests contain mechanisms that allow pipes to sound when called upon from the console. In a mechanical key action or tracker organ, the keyboards (or manuals) at the console are mechanically linked to pallets that permit or block the flow of wind to all ranks of any given note in each division. With modern electric action chests, the pallets or pneumatic valves are controlled electrically via an electronic switching system.
Organ chests are generally rectangular in shape; minimum dimensions are 8’ long, 12” thick and 3’ wide but wind chests on sizeable instruments can be significantly larger. One or more passage boards measuring at least 12” wide should run the entire length of the chest for reasonable tuning and service access. Further, a clearance of 42” under each chest is desirable to access the wind chest’s internal mechanisms from the underside.
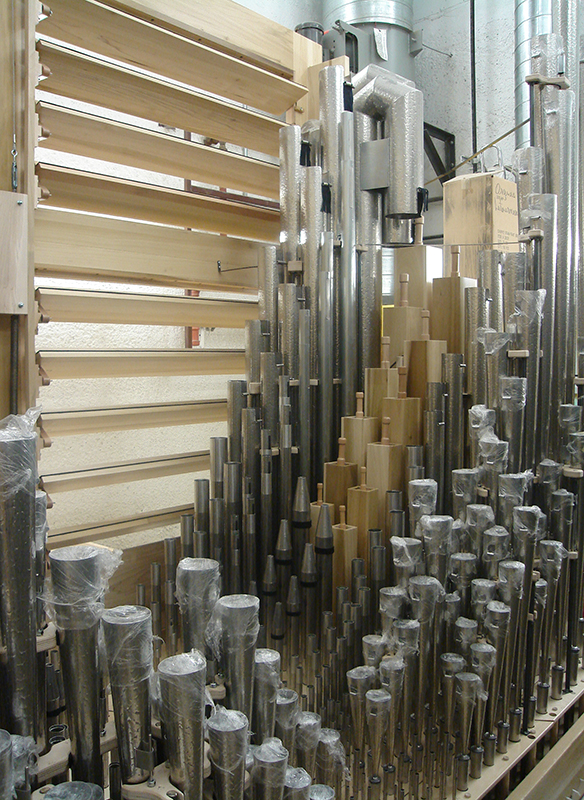
The wind that sounds the organ’s pipes is produced by an organ blower and channelled throughout the organ via wind lines. Blowers range in size depending on the wind capacity and wind pressures required; their electric motors can be rated from less than 1 horsepower to over 10 horsepower and usually require a three-phase electrical connection. Wind reservoirs serve to stabilize the wind flow from the blower and are located at strategic locations within the wind system; they resemble rectangular boxes with floating tops held in place via torsion or coil springs. Many organs also incorporate schwimmer-style wind regulators built into the underside of the organ’s wind chests to further regulate the wind pressure within each chest.
Some divisions of the organ are built within expression boxes or enclosures. These boxes are similar to a room made out of solid wood panels and will follow the perimeter of the entire division. One or more of the enclosure’s walls will have louvers that open or close in response to the organist’s commands at the console, allowing an invaluable element of dynamic control.
A pipe organ if it could be seen from a bird’s-eye view will usually have a rectangular footprint with the width typically exceeding the depth. The space required for a pipe organ can be roughly calculated using the number of 10 square feet per stop, assuming a 20’ ceiling. When the ceiling is over 20’ high, it may be possible to double-deck divisions, meaning placing one division on top of another. The weight of an organ is generally 600 lb per stop which calculates to a load of 60 lb per square foot. In cases where divisions are stacked, the load doubles to 120 lb per square foot.
Need more information?
Contact our experts